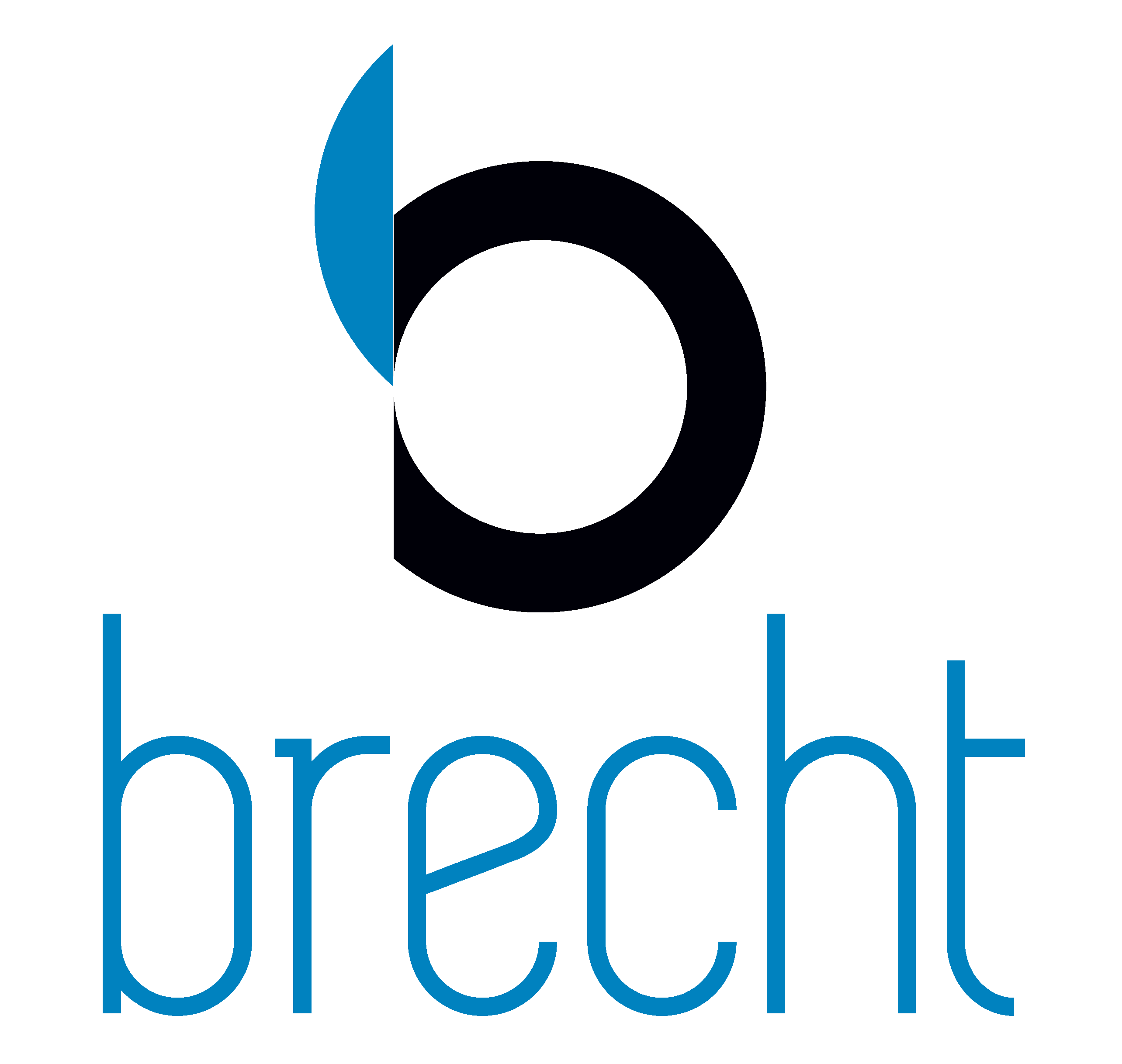
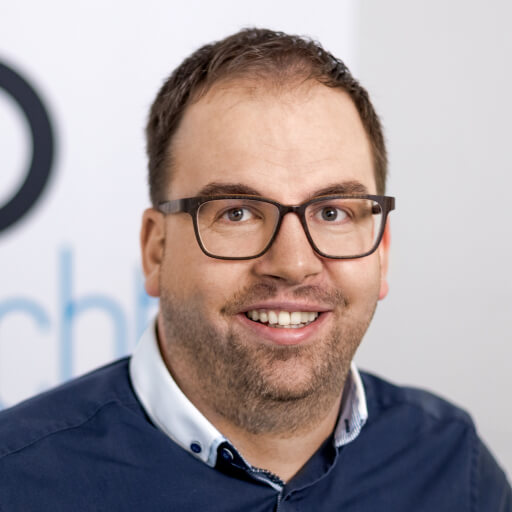
Thanks to RobCo, we can multiply our machine utilisation rates and thus offer attractive hourly rates for series parts on the market. Thanks to the option of multiple zero points, RobCo can be used flexibly on different machines. This leads to cost savings during retooling.
More time for quality control
The operating and maintenance costs of CNC machines are constantly rising, so maximum capacity utilization is crucial to remain competitive. However, Brecht was faced with the challenge of sickness-related absences hindering the continuous loading of the machines. RobCo's modular robots offered a solution to this problem.
Working with RobCo, Brecht aimed to increase their productivity and maximize machine utilization.
With the help of RobCo, Brecht was able to implement modular robots for night and weekend shifts and compensate for employee absences due to illness. In addition, the robots could be connected to different machines due to their flexibility. This allows employees to concentrate more on quality control and preparing subsequent orders while the robots load the machines.
Increased efficiency and machine utilization
A key advantage of integrating RobCo for Brecht was the flexible design of the robots, which have different arm lengths and numbers of axes. In addition, several zero points (zero point: parts warehouse and zero point: different machines) could be defined.
Thanks to the RobCo robots, individual parts can now be produced during the day and series parts manufactured at night, which leads to a significant increase in efficiency and production as well as utilization of the production facilities. Thanks to the flexible use of the robots on different machines, machine utilization has increased three- to four-fold since implementation, which saves Brecht considerable costs.