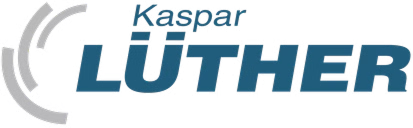
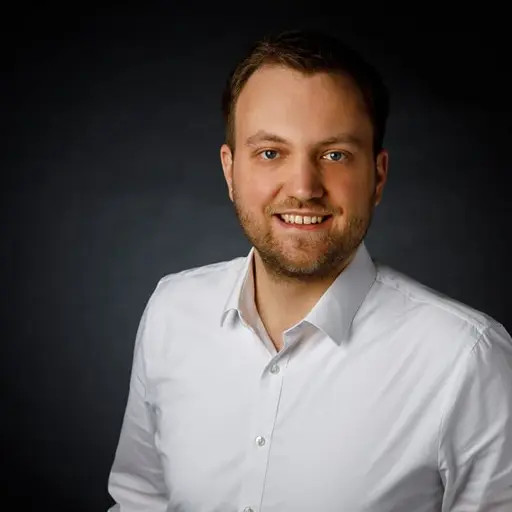
We deliberately chose RobCo as our partner and are thrilled with the collaboration and successful implementation. We were looking for an automation solution that takes an unconventional yet highly flexible approach to automation. RobCo's concept is also scalable and is already contributing to noticeably improved production capacity utilization.
Kaspar Lüther GmbH increases efficiency and production capacity with RobCo.
Kaspar Lüther GmbH & Co. KG is a specialist in high-quality and technically sophisticated zinc die casting in small series. Subsequent CNC processing of the castings results in components with the tightest tolerances and the highest quality standards. The flexible corporate structure enables tailor-made complete solutions, which start in the planning and project phase through personal and intensive advice.
The challenge
Kaspar Lüther was looking for a flexible automation partner who was ready to find an unconventional and flexible way of automation. The central process step that had to be automated was particularly demanding:
- The die-cast raw part had to be inserted into the first CNC lathe and processing started
- The component then had to be clamped to the machined diameter in a second CNC lathe and cleaned of chips and coolants after turning
The biggest challenge: No standard solution on the market was able to automatically map this process in the desired form. In addition, the existing lathes had no interfaces and no automated doors, which made conventional integration difficult.
The solution
RobCo impressed with the most flexible solution on the market, which not only enabled complete automation of the processing cycle, but was also attractively priced.
- Automation of the entire process — from part collection to processing to final cleaning
- Integration of existing lathes without interfaces through intelligent actuator control
- Automated door opening of lathes to ensure smooth component handling
- Scalable robotic solution, which can be easily duplicated for other processes in the company
Thanks to this custom implementation, RobCo was able to offer a solution that could be perfectly integrated into the existing production processes of Kaspar Lüther GmbH.
The results
Since implementing the RobCo solution, the company has been able to significantly optimize its production:
- Maximum use of resources — A worker can now be deployed parallel to other activities; only the regular measurement process is required manually.
- Expanded production capacity — Thanks to automation, Kaspar Lüther can operate the plant in normal shifts without using additional personnel.
- Higher efficiency and cost savings — Automation not only eliminated bottlenecks, but also made the entire manufacturing process more economic and stable.
Conclusion
The collaboration between Kaspar Lüther GmbH and RobCo clearly demonstrates how highly complex production processes can be made efficient and future-proof through tailor-made automation solutions. Flexible, efficient and scalable — automation that grows with you.